Exploring the Key Technologies and Application Advantages of Automatic Stator Winding Machines
Stators are critical components in electric motors, generators, and transformers, where copper windings convert electrical energy into mechanical motion (or vice versa). The precision of these windings directly impacts performance, efficiency, and durability. Automatic stator winding machines have revolutionized this manufacturing step, replacing labor-intensive manual processes with advanced automation. From servo-driven precision to AI-powered quality control, these machines offer unprecedented accuracy and productivity. Let’s explore the key technologies driving automatic stator winding machines and their advantages across industries.
Core Technologies Powering Automatic Stator Winding Machines
Servo Motor Control Systems
At the heart of automatic stator winding machines lies servo motor technology, which enables precise control over winding speed, tension, and position. Unlike traditional induction motors, servo motors use feedback loops (via encoders) to adjust motion in real time, ensuring consistent wire placement. For example, when winding a stator with 500+ slots, the machine can align the wire within 0.01mm of the target position, even at high speeds (up to 3,000 revolutions per minute). This precision prevents wire overlap, which can cause short circuits, and ensures uniform tension—critical for reducing energy loss in the final motor.
Modern systems use multi-axis servo controls, allowing simultaneous movement of the stator, wire guide, and tensioner. This synchronization is vital for complex wind patterns, such as concentric or distributed windings, where each slot requires a specific number of turns. Servo technology also enables “soft start/stop” functionality, eliminating wire breakage during acceleration or deceleration—a common issue in older mechanical machines.
Intelligent Wire Tension Management
Maintaining consistent wire tension is essential for high-quality windings. Too much tension stretches or thins the wire, weakening it; too little leads to loose, uneven windings that vibrate and overheat. Automatic stator winding machines address this with advanced tensioners, often paired with AI algorithms.
Load-cell-based tensioners measure wire tension 1,000+ times per second, adjusting in milliseconds to compensate for changes in wire diameter or spool size. For example, when the wire spool nears empty, the system detects the slight tension drop and increases brake pressure on the spool to maintain stability. AI enhances this further by learning from past runs—if a specific wire type (e.g., enameled copper) tends to stretch at high speeds, the machine adjusts tension proactively for future batches.
Vision Systems and Quality Inspection
Defects like missed slots, wire crossings, or insulation damage can render a stator useless. Automatic stator winding machines integrate high-resolution vision systems to catch these issues in real time. Cameras mounted above and below the stator capture images during and after winding, with machine learning algorithms analyzing the data to detect anomalies.
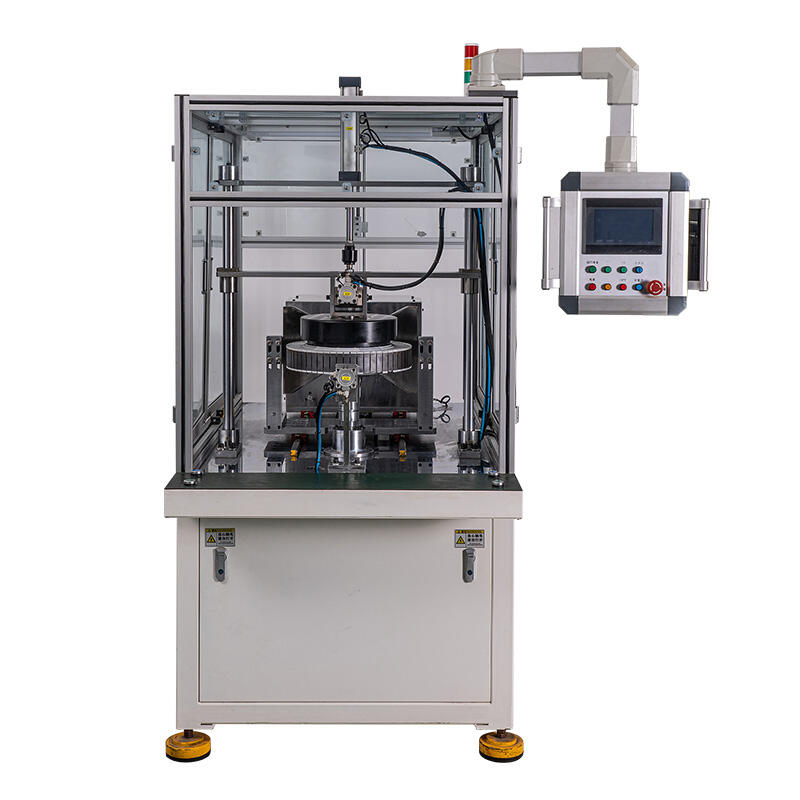
For instance, a vision system can count wire turns per slot, ensuring compliance with design specifications (e.g., 25 turns for a motor stator). It flags underfilled or overfilled slots instantly, stopping the machine to prevent wasted materials. Post-winding, it checks for insulation cracks or uneven layer heights—critical for motors in high-voltage applications like electric vehicles (EVs). This reduces reliance on manual inspection, which is slower and prone to human error.
Flexible Programming and Quick Changeovers
Stators vary widely in size (from small appliance motors to large industrial generators) and winding patterns. Automatic stator winding machines handle this diversity with user-friendly programming interfaces and modular tooling. Operators can load pre-saved winding programs for common stator types, or create new ones via touchscreen interfaces, inputting parameters like slot count, turns per slot, and wire diameter.
Quick-change tooling—such as interchangeable mandrels and wire guides—cuts changeover time from hours (in manual machines) to minutes. This flexibility is invaluable for manufacturers producing multiple stator models, allowing them to switch between residential HVAC stators and EV motor stators efficiently. Some advanced machines even auto-calibrate tooling after changes, ensuring accuracy without manual adjustments.
Application Advantages Across Industries
Electric Vehicle (EV) Manufacturing
EV motors demand stators with ultra-precise windings to maximize range and efficiency. Automatic stator winding machines deliver this by:
- Producing windings with 99.9% accuracy, reducing energy loss in the motor.
- Handling high-volume production (up to 500 stators per hour) to meet EV demand.
- Supporting hairpin windings—a complex design that increases copper density—with robotic arms bending and inserting pre-formed wires into slots. This technology, unique to automatic machines, boosts motor efficiency by 5–10% compared to traditional windings.
Home Appliances
From refrigerators to washing machines, small motors rely on cost-effective, consistent stators. Automatic machines lower production costs by:
- Reducing labor requirements—one operator can oversee 2–3 machines, vs. 1 operator per manual machine.
- Minimizing scrap rates (often below 1%) through real-time quality checks.
- Enabling high-speed winding for mass-produced stators, keeping up with appliance assembly lines.
Renewable Energy Generators
Wind turbines and solar inverters use large stators that require durable, high-tension windings. Automatic stator winding machines excel here by:
- Handling thick gauge wires (up to 10mm diameter) with robust tensioners, ensuring windings withstand vibration in turbines.
- Producing distributed windings that optimize magnetic flux, increasing generator efficiency.
- Integrating with downstream processes (e.g., impregnation) via conveyor systems, streamlining production.
FAQ: Automatic Stator Winding Machines
How do automatic stator winding machines compare to manual winding in terms of speed?
Automatic machines are 5–10x faster. A manual operator might wind 20–30 small stators per hour, while an automatic machine can produce 100–300 per hour for the same size. For large stators, the gap is even wider—automatic systems handle 10–15 per hour vs. 1–2 manually.
Can these machines handle different wire types, like enameled copper or aluminum?
Yes. They adjust tension, speed, and tooling for various wires. Enameled copper (common in EVs) requires gentle handling to avoid insulation damage, while aluminum (used in cost-sensitive appliances) needs higher tension to prevent slippage. AI algorithms adapt settings based on wire material.
What’s the typical ROI for investing in an automatic stator winding machine?
ROI ranges from 1–3 years, depending on production volume. Labor savings (reduced operators), lower scrap rates, and increased throughput drive this. For a mid-sized EV supplier, replacing 5 manual stations with 1 automatic machine can save $200,000+ annually.
How complex is training for operators?
Modern machines are user-friendly—operators with basic technical skills can learn programming and maintenance in 1–2 weeks. Manufacturers often provide on-site training, and many machines include troubleshooting guides via touchscreens.
Are automatic stator winding machines suitable for small-batch production?
Yes. Quick changeovers and flexible programming make them viable for batches as small as 50 units. While manual machines may seem cheaper for tiny runs, automatic systems reduce errors and rework, offsetting costs even at low volumes.
Table of Contents
- Exploring the Key Technologies and Application Advantages of Automatic Stator Winding Machines
- Core Technologies Powering Automatic Stator Winding Machines
- Application Advantages Across Industries
-
FAQ: Automatic Stator Winding Machines
- How do automatic stator winding machines compare to manual winding in terms of speed?
- Can these machines handle different wire types, like enameled copper or aluminum?
- What’s the typical ROI for investing in an automatic stator winding machine?
- How complex is training for operators?
- Are automatic stator winding machines suitable for small-batch production?