Automatic Stator Winding Machines: Paving the Way for Intelligent Motor Production
Intelligent motor production—where precision, efficiency, and data-driven decision-making converge—relies on advanced manufacturing tools that transcend traditional automation. At the heart of this transformation are automatic stator winding machines, which have evolved from simple wire-wrapping devices into interconnected systems that optimize every step of stator production. By integrating AI, IoT, and robotics, these machines are not just speeding up manufacturing but redefining what’s possible in motor performance. Let’s explore how automatic stator winding machines are enabling the shift to intelligent motor production and why they’re becoming indispensable in modern factories.
The Intelligent Edge: How Automation Transforms Stator Production
Intelligent motor production demands more than consistent windings—it requires systems that adapt, learn, and communicate. Automatic stator winding machines deliver on all fronts, thanks to three key technological pillars:
AI-Driven Process Optimization
Modern automatic stator winding machines use artificial intelligence to analyze production data in real time, making micro-adjustments to ensure optimal results. For example, during high-volume production runs, AI algorithms track variables like wire tension, winding speed, and stator temperature. If a pattern emerges—such as increased wire breakage when winding at 2,500 RPM—the system automatically reduces speed by 5% and adjusts tension, preventing defects before they occur.
AI also optimizes winding patterns for specific motor types. For a high-efficiency EV motor, the machine might recommend a concentrated winding layout that reduces energy loss by 3%, based on historical data from thousands of successful runs. This level of customization, once reserved for premium motors, is now accessible to mass production lines, thanks to AI’s ability to process complex design parameters quickly.
IoT Connectivity and Smart Factory Integration
Automatic stator winding machines are no longer standalone units—they’re critical nodes in interconnected smart factories. Equipped with IoT sensors, these machines collect and share data on production metrics (e.g., cycles per hour, defect rates) and equipment health (e.g., servo motor temperature, bearing vibration). This data feeds into central manufacturing execution systems (MES), allowing plant managers to monitor production in real time from anywhere in the world.
For example, if a machine in a Chinese factory detects a 10% drop in winding precision, the MES can alert technicians in Germany, who can troubleshoot remotely via a secure dashboard. Predictive maintenance is another key benefit: IoT sensors track wear on critical components like wire guides, sending alerts when replacement is needed—often weeks before a breakdown would occur. This reduces unplanned downtime by up to 30% compared to traditional maintenance schedules.
Robotics and Flexible Automation
Intelligent motor production requires adaptability, especially as manufacturers shift between motor models for different applications (e.g., from a 10kW industrial motor to a 5kW EV motor). Automatic stator winding machines, paired with robotic systems, enable seamless changeovers in under 15 minutes—down from 2 hours with semi-automatic setups.
Robotic arms load and unload stators, adjusting grippers to fit different sizes without manual intervention. Vision-guided robots inspect windings post-production, comparing results to 3D models of perfect stators and flagging even minor deviations (e.g., a 0.1mm misalignment in a hairpin winding). This integration of robotics and automation ensures that intelligent factories can handle high-mix, high-volume production without sacrificing quality.
Enhancing Motor Performance Through Precision
The quality of a motor’s stator directly impacts its efficiency, durability, and energy consumption. Automatic stator winding machines elevate motor performance by achieving levels of precision impossible with manual or semi-automatic methods:
- Uniform Tension Control: Maintaining consistent wire tension (within ±0.5N) ensures that each turn contributes equally to the motor’s magnetic field, reducing energy loss by up to 5% compared to unevenly wound stators. This is critical for EVs, where every percentage point of efficiency extends range.
- Complex Winding Patterns: Intelligent machines excel at intricate designs like hairpin windings, which pack 20% more copper into the same stator volume. This increases motor power density, allowing automakers to use smaller, lighter motors without sacrificing performance. For example, a hairpin-wound stator in a Tesla Model 3 motor contributes to its 396-mile range.
- Minimized Waste: AI-powered systems calculate the exact length of wire needed for each stator, reducing scrap by 15–20%. This not only cuts material costs but also aligns with sustainable manufacturing goals, a priority for brands aiming to reduce their carbon footprint.
From Stator to Smart Motor: End-to-End Intelligence
Automatic stator winding machines are the starting point of a connected production chain that transforms stators into fully intelligent motors. Post-winding, stators move to assembly lines where they’re integrated with rotors, sensors, and control systems—all tracked by the same IoT network used by the winding machines.
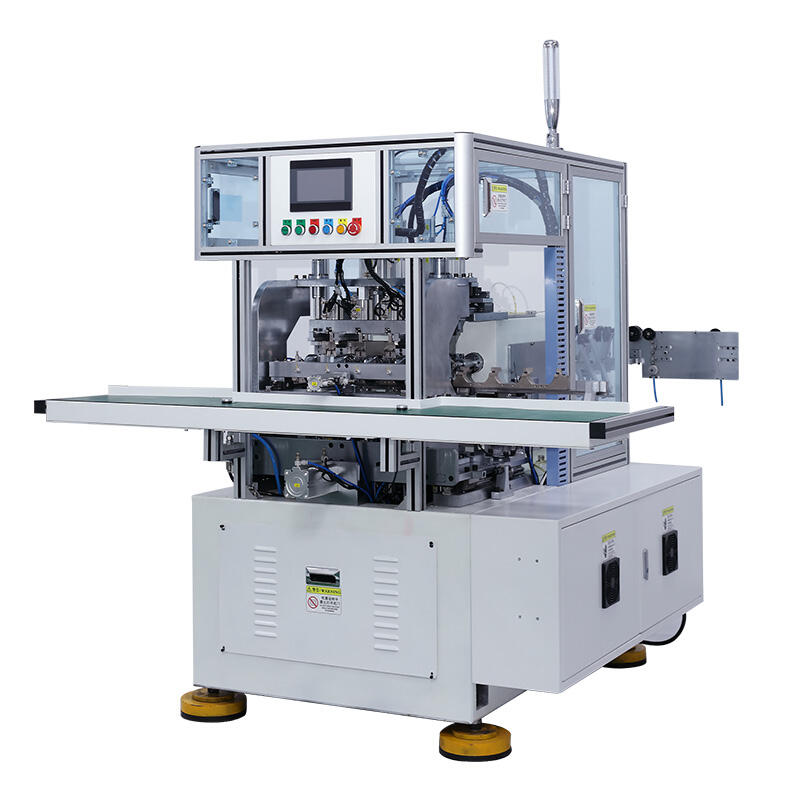
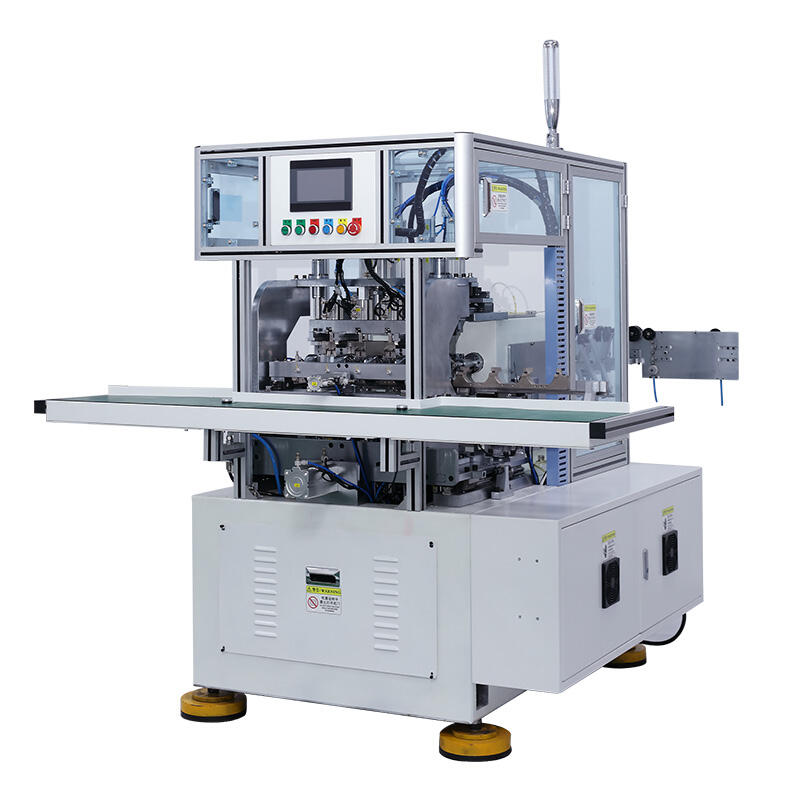
This end-to-end connectivity ensures traceability: every motor can be linked back to its stator’s production data, including winding parameters, inspection results, and even the batch of wire used. If a motor fails in the field, manufacturers can analyze the stator’s winding history to identify root causes, improving future production runs.
In intelligent factories, this data also feeds into digital twins—virtual replicas of the motor production process. Engineers can simulate changes (e.g., adjusting winding tension) in the digital twin before implementing them on the factory floor, reducing trial-and-error costs by 40%.
FAQ: Automatic Stator Winding Machines in Intelligent Production
How do automatic stator winding machines integrate with other smart factory systems?
They connect via standard protocols like OPC UA or MQTT, sharing data with MES, ERP, and predictive maintenance platforms. For example, production targets from the ERP system automatically adjust the machine’s output, while quality data from the winding machine updates the MES in real time.
Can these machines handle the tiny stators used in medical devices or drones?
Yes. High-precision models with micro-winding capabilities handle wires as thin as 0.02mm, producing stators for 10W drone motors or 5W medical pump motors. AI ensures consistent tension even with delicate wires, preventing breakage.
What skills do operators need to manage intelligent automatic stator winding machines?
Basic programming and data analysis skills are key, but modern interfaces simplify tasks: operators use touchscreens to load winding programs, and AI-driven dashboards highlight issues (e.g., “Tension spike detected—check wire spool”). Manufacturers often provide training in IoT integration and predictive maintenance basics.
How much energy do automatic stator winding machines save compared to manual methods?
While the machines themselves consume more electricity than manual tools, the energy saved in motor production (via reduced rework) and in the motors’ lifecycle (via higher efficiency) far outweighs this. A study found that intelligent winding systems result in a net energy savings of 12% per motor over its lifetime.
Are automatic stator winding machines suitable for small-scale intelligent production?
Yes. Compact models with IoT capabilities are available for workshops producing 50–100 stators daily. Cloud-based AI features (accessible via subscription) allow small manufacturers to leverage the same optimization algorithms used by large factories, leveling the playing field.
Table of Contents
- Automatic Stator Winding Machines: Paving the Way for Intelligent Motor Production
-
FAQ: Automatic Stator Winding Machines in Intelligent Production
- How do automatic stator winding machines integrate with other smart factory systems?
- Can these machines handle the tiny stators used in medical devices or drones?
- What skills do operators need to manage intelligent automatic stator winding machines?
- How much energy do automatic stator winding machines save compared to manual methods?
- Are automatic stator winding machines suitable for small-scale intelligent production?