From Manual to Automatic: The Transformation of Stator Winding Machines and Market Prospects
Stator winding machines have come a long way from their humble manual origins, evolving into sophisticated automated systems that power modern manufacturing. This transformation has been driven by the growing demand for precision, efficiency, and scalability in industries ranging from automotive to renewable energy. As stator designs become more complex and production volumes surge, the shift from manual to automatic stator winding machines has become not just a choice but a necessity. Let’s explore this journey of innovation and the promising market prospects that lie ahead.
The Era of Manual Stator Winding: Limitations and Challenges
Not long ago, stator winding was a labor-intensive craft, relying heavily on skilled workers to thread copper wire through stator slots by hand. Manual stator winding machines—essentially simple jigs or hand cranks—required operators to count turns, maintain tension, and ensure uniform placement, all while working against tight production deadlines.
This approach had inherent limitations:
- Inconsistency: Even skilled operators produced variations in winding tension and turn counts, leading to stators with uneven performance. A slight difference in wire placement could cause motors to vibrate, overheat, or fail prematurely.
- Low Efficiency: A single worker could wind only 10–20 small stators per hour, making high-volume production nearly impossible. For large stators (e.g., those used in industrial generators), the process could take hours per unit.
- High Labor Costs: Skilled winding operators commanded premium wages, and training new workers took months. Turnover was costly, as new hires often produced subpar windings initially.
- Safety Risks: Repetitive motions led to ergonomic injuries, while sharp wire ends and rotating parts posed physical hazards.
Manual stator winding machines persisted in small-scale workshops and low-volume production for decades, but by the early 2000s, the rise of mass-produced appliances and electric motors exposed their inadequacies. As demand for reliable, high-performance stators grew, manufacturers began seeking automated solutions.
The Rise of Automation: Key Milestones in Stator Winding Machine Evolution
The transition from manual to automatic stator winding machines unfolded in stages, with each innovation addressing specific pain points of the manual era.
Semi-Automatic Machines: Bridging the Gap
Semi-automatic stator winding machines emerged in the 1990s as an intermediate step. These systems automated core functions like wire feeding and turn counting but still required operators to load/unload stators and guide wires into slots. For example, a semi-automatic machine might use a mechanical arm to feed wire while the operator positioned the stator, reducing human error in turn counts but retaining the need for skilled labor.
This phase introduced basic electronic controls, allowing operators to set parameters like turns per slot via dials or simple keypads. While faster than manual methods (producing 30–50 small stators per hour), semi-automatic machines still struggled with complex winding patterns and consistency, paving the way for full automation.
Fully Automatic Systems: Precision and Productivity
By the 2010s, advancements in servo motors, sensors, and computing power enabled fully automatic stator winding machines. These systems eliminated most manual intervention, handling everything from loading stators to quality inspection.
Key breakthroughs included:
- Multi-axis servo control: Enabling precise coordination of wire guides, stator rotation, and tensioners to handle complex wind patterns like hairpin or concentrated windings.
- Integrated vision systems: Using cameras and AI to verify wire placement and detect defects in real time, reducing reliance on post-production inspections.
- Quick-change tooling: Allowing manufacturers to switch between stator models in minutes, a critical feature as product diversification accelerated.
Today’s automatic stator winding machines can produce up to 500 small stators per hour with 99.9% accuracy—numbers unimaginable with manual methods. They handle wires as thin as 0.05mm (for micro-motors) and as thick as 10mm (for industrial generators), adapting to materials from enameled copper to aluminum with minimal setup.
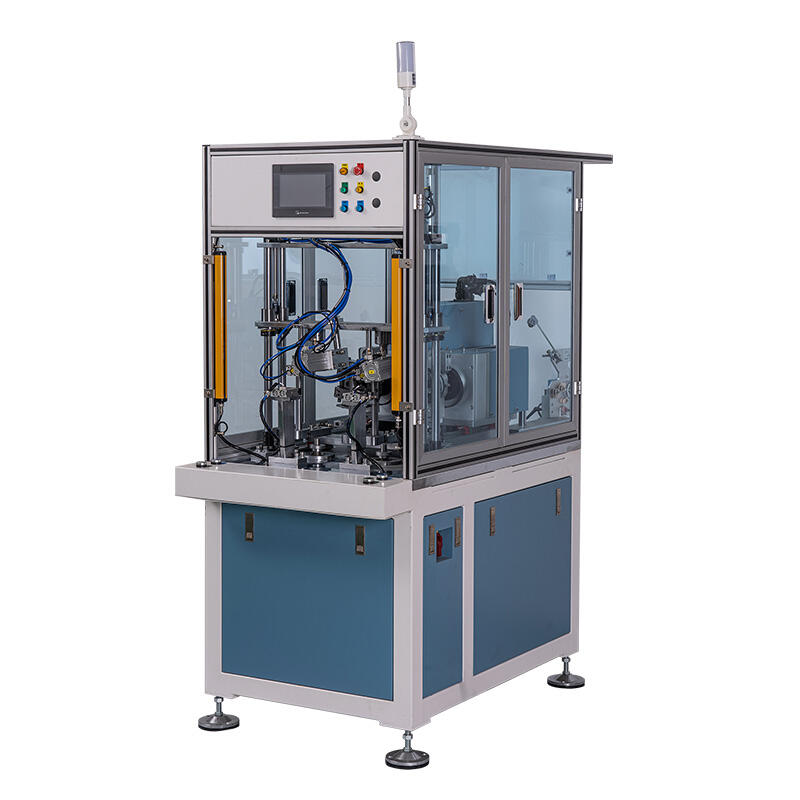
Market Drivers: Why Automatic Stator Winding Machines Are in High Demand
The global stator winding machine market is projected to grow at a CAGR of 7.2% from 2024 to 2030, driven by several key trends:
Electric Vehicle (EV) Boom
EVs require high-performance motors with densely wound stators to maximize range and efficiency. Traditional manual winding can’t meet the precision or volume demands of EV production—for example, a single EV motor stator may require 1,000+ turns of ultra-thin wire with zero defects. Automatic stator winding machines, especially those capable of hairpin winding (which increases copper density by 20%), have become essential for EV manufacturers. Companies like Tesla and BYD rely on automated lines to produce 10,000+ stators daily, fueling demand for advanced machines.
Renewable Energy Expansion
Wind turbines and solar inverters depend on large, durable stators that can withstand harsh conditions. Automatic stator winding machines produce windings with consistent tension and turn counts, ensuring generators operate efficiently for 20+ years. As countries shift to renewable energy, wind turbine production is soaring—each turbine requires multiple stators, driving demand for heavy-duty automatic machines.
Home Appliance Growth
The rise of smart appliances (e.g., energy-efficient refrigerators, robotic vacuum cleaners) has increased demand for small, high-precision stators. Automatic machines enable cost-effective mass production, with features like quick changeovers allowing manufacturers to switch between stator models for different appliances. In China, the world’s largest appliance market, stator winding machine sales grew 15% in 2023 alone, driven by this trend.
Industrial Automation
Factories are increasingly adopting automated systems, from conveyor belts to robotic arms, all powered by electric motors. These motors require reliable stators, and manufacturers are turning to automatic winding machines to ensure consistency. The shift toward “smart factories” also favors connected automatic machines, which integrate with IoT systems for predictive maintenance and production tracking.
Market Challenges and Opportunities
While the outlook is bright, the stator winding machine market faces challenges:
- High Initial Costs: Automatic machines can cost 5–10x more than manual ones, deterring small manufacturers in price-sensitive markets. However, falling costs of servo motors and AI components are making automation more accessible.
- Skill Gaps: Operating advanced machines requires training in programming and troubleshooting, which is scarce in some regions. Manufacturers are addressing this with user-friendly interfaces and remote training programs.
Opportunities abound for innovation:
- AI and Machine Learning: Future machines will predict maintenance needs, optimize winding patterns for energy efficiency, and adapt to new materials (e.g., superconducting wires).
- Sustainability: Machines that reduce copper waste (by minimizing scrap) or use energy-efficient components will gain traction as manufacturers prioritize green production.
FAQ: Stator Winding Machines Market
What is the current size of the stator winding machine market?
The global market was valued at 1.2 billion in 2023 and is expected to reach 2 billion by 2030, driven by EV and renewable energy demand.
Which regions are leading in stator winding machine adoption?
Asia-Pacific dominates, accounting for 60% of sales, led by China, Japan, and South Korea—key hubs for EV and appliance production. Europe and North America are growing rapidly, fueled by EV manufacturing and renewable energy projects.
Are manual stator winding machines still relevant?
Yes, but in niche markets: small-batch production (e.g., custom motors for vintage cars), low-cost regions with cheap labor, or repairs. However, even these segments are gradually shifting to semi-automatic machines for better consistency.
How do hairpin winding machines differ from traditional automatic machines?
Hairpin machines use pre-formed, U-shaped wires (resembling hairpins) inserted into stator slots, then welded together. This method increases copper density and motor efficiency, making it ideal for EVs. Traditional machines wind continuous wire, which is simpler but less efficient for high-performance motors.
What’s the average lifespan of an automatic stator winding machine?
With proper maintenance, automatic machines last 10–15 years. Servo motors and vision systems may need replacement after 5–7 years, but modular designs make upgrades cost-effective.
Table of Contents
- From Manual to Automatic: The Transformation of Stator Winding Machines and Market Prospects
- The Rise of Automation: Key Milestones in Stator Winding Machine Evolution
-
FAQ: Stator Winding Machines Market
- What is the current size of the stator winding machine market?
- Which regions are leading in stator winding machine adoption?
- Are manual stator winding machines still relevant?
- How do hairpin winding machines differ from traditional automatic machines?
- What’s the average lifespan of an automatic stator winding machine?